In today’s automation trend, the bar feeding process in mechanical production helps improve machine usage efficiency, productivity, and labor quality.
1. General introduction to automatic bar feeding using a Gantry robot
Currently, in the production, assembly, and product quality inspection in the industry in general and the mechanical manufacturing industry in particular, everything is all developing according to the rising trend of automation. To ensure a stable production process, it is necessary to supply workpieces accurately in time and space and continuously in cycles in a systematic and highly reliable manner. Therefore, the bar feeding process is one of the urgent requirements that need to be researched and resolved in automatic production systems with the aim of improving productivity, labor quality, and machine usage efficiency.
In addition to robotic arms, robots fixed above the surface are also widely used in these systems. Gantry robots often appear in mass production lines, with large productivity because they are not limited by operating area.
In mechanical processing machines, to optimize production and increase productivity and product quality, there will be different bar feeding methods for each type of product. In particular, for CNC lathes, there are two main automatic bar feeding methods: Bar feeder and Gantry robot. In this topic, we would like to introduce the Gantry robot bar feeding solution.
2. Structure and technical specifications
2.1 Structure
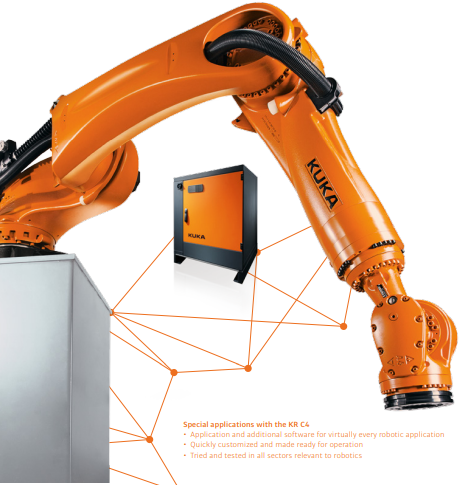
The general structure of the system includes Guide rail system – transmission, signal control cable, control cabinet and industrial computer, sensors, drive motor, and robot gripper.
2.2 Main technical parameters
3. Characteristics, advantages, and main components of the system
3.1 Characteristics
- The system is used to supply each workpiece during the machining process with a fixed size (each product has a separate gripper structure). Compressed air is an indispensable element in the equipment’s requirements for the system to operate smoothly and accurately. Compressed air needs to be dry, clean, oil-free, and water-free. Short bar feeding time helps increase machining output.
- Gantry Robot solves both problems: unlimited scale and movement area, as well as space-saving, are the two biggest characteristics of Gantry Robots that are widely used in automation systems.
- In addition, simple design, reasonable cost, and easy scalability due to the modular structure are additional features that add competitive strength to Gantry Robots.
3.2 Advantages
- Optimally utilize up to 96% of installation space to perform tasks related to pumping and applying glue, saving space and simple design.
- Easily scale in all 3 dimensions: X, Y, and Z.
- Due to its sturdy yet compact structure, the Gantry robot operates accurately through many iterations.
- Modular design, therefore, has options suitable for each user’s unique application, saving maintenance and periodic inspection costs.
- Combine with image sensor modules in some product lines to increase accuracy, post-machining inspection, and NG product rejection.
3.3. Main components of the system
a. KR-C4 control system
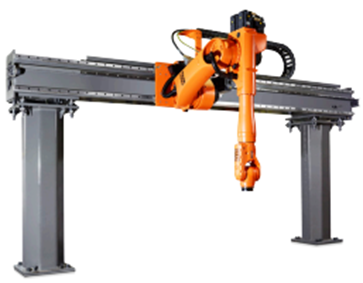
- The KR C4 controller is a pioneer in automation.
- It reduces your costs for integration, maintenance, and servicing. At the same time, the long-term efficiency and flexibility of the systems are increased – thanks to industry standards.
- KR C4 software architecture integrates Robot Control, PLC Control, Motion Control (e.g., KUKA.CNC), and Safety Control. All controllers share a database and infrastructure.
- Higher efficiency in CNC machining. The KUKA.CNC control option allows direct programming and operation of the KUKA robot via G-code. It can handle even the most complex programs from CAD/CAM systems and provides the highest accuracy due to CNC toolpath simulation. This dramatically simplifies the integration of the robot into an existing CNC environment.
b. Smart PAD controller
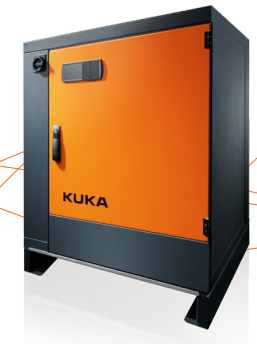
- Whether you’re a programming novice or an expert, the KUKA smart PDA will quickly get you to your goals because it offers suitable programming options for every requirement.
- A single dashboard to perform the most diverse tasks reliably.
- KUKA.KRL – advanced robot programming language. “KUKA Language Robotics” is a globally standard programming language. It is easy to learn and fits perfectly with KUKA robots’ diverse options.
- The intuitive KUKA smartPAD can be used to create complex and customized programs for robot movements and tasks in a variety of applications – both online and offline.
- Simple and efficient: programming with inline forms, forms to program tasks and movements quickly, without errors. They can be ordered via the menu and are available as standard. This simplifies the programming of RoboTeams with up to six synchronized robots.
- Customer-defined program modules. Upon customer request, KUKA integrators can expand the library of available KUKA inline templates. This leads to the creation of special applications that can be easily programmed for recurring tasks.
- Competitive advantage for system integrators: specially developed inline forms enable unique solutions that are optimally suited to the companies that use them.
Our company always wishes to become a reliable partner and a leading supplier of equipment and solutions for the success of our customers. For more detailed information, please contact:
MITAS Hanoi Technology JSC
Address: 5th Floor, C’Land Building, No. 81 Le Duc Tho St., My Dinh 2 Ward, Nam Tu Liem Dist., Hanoi, Vietnam
Web: https://mitas.vn | Tel: (+84) 243 8585 111 | Email: sales@mitas.vn
The trust and support of our customers are a driving force and an invaluable asset to our company. We sincerely thank you./.